Overview
Kemerton Silica Sand ore is mined by dredging. This has proved to be the most economical and environmentally friendly option available.
The ore is pumped by the dredge to our ROM storage area where it is stockpiled and sampled ready for blending into our processing plant.
Front end loaders blend the ore into the processing plant where it is washed, screened and any heavy mineral content is removed. Emphasis is on a quality product and a number of quality tests are carried out during this process.
Mining
Before mining commences, a comprehensive drilling program is undertaken to determine the suitability of the resource.
The topsoil is removed and respread over previously mined and reshaped areas. This process greatly improves the quality of rehabilitation and ensures that natural vegetation is re-established.
The top 3.5m of sand resource is treated as overburden and this is removed by a dredge if below the watertable or as a dry mining operation using trucks and loaders. The overburden is used to reshape previously mined areas.
Alternatively, the top 3.5m may be used as a feed stock for the low AL203 product. The remainder of the ore body is dredged in two intervals to manage variations in AL203 and Fe203concentrations.
The ore is pumped from the dredge to the main processing plant, removing any rocks, clay or large impurities via a scalping screen.
The ore is de-watered via cyclones and stockpiled according to grade for subsequent quality control blending feedstock into the processing plant.

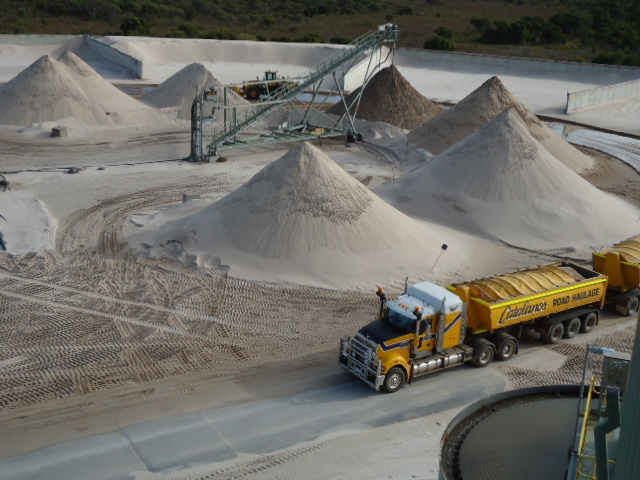
Processing
The quality control program focuses on managing the alumina content. The ore blending aims to produce consistent alumina levels in the product to suit customer specifications.
The sand is reclaimed from the plant feed stockpiles by front end loader and deposited in the plant feed bin.
The feed passes through the main processing plant where it is sized and the heavy minerals removed according to customer requirements.
The final product is stacked and left to drain to achieve a final moisture content of less than 5%.
After final analysis confirms that the product meets specification, a finished stockpile is loaded onto trucks and transported to the Bunbury Port.
Production capacity at the present plant configuration is approximately 550,000 tonnes per annum.
There are three main areas of focus in our quality control management system; Chemical composition of the sand, size composition and the removal of heavy minerals.
The chemical make up of the sand is controlled through a rigorous sampling procedures, as per our quality control section.
Sizing is controlled firstly via our primary screening which removes coarse particles. The product then enters our flat bottom classifiers where product size is determined. Finally a positive screening takes place by passing all the product through five submerged trommels.
Heavy minerals such as TiO2 and Fe2O3 are removed via cyclones and a three stage spiral circuit. Attritioners and a WHIMS electromagnet are also part of the process for removal of Fe2O3.